Considering pressure vessel design methods for a tapered shell (the rail is not a parrallel-wall cylinder) and reducing the material properties for the aluminium by a big chunk to take account for it not being 'good' aluminium meant that I did not want to dig into pressure retaining wall thickness.
All things considered I don't think I could do a better job of making a totally fresh part in terms of weight or function unless I want to change the Fuel Pressure Regulator arrangement. Even then a FPR blanking plate would still be a better solution if an external FPR was going to be used, so the GM part is living on.
But there is still redundant metal in there that is not taking any load.
0.623kg starting weight:
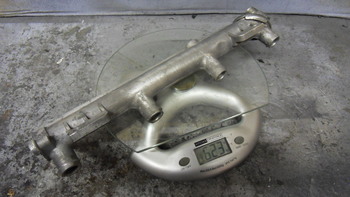
Casting runner pad marked for removal:
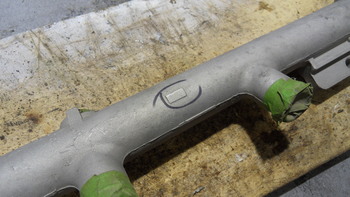
Casting flash for cleaning up:
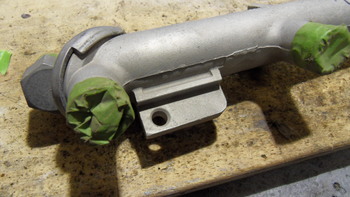
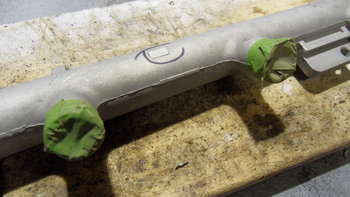
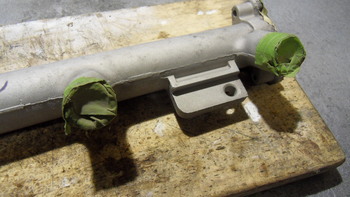
The fixing brackets have one hole each to attach them to the top of the cylinder head and the bolts act in a combined tension and shear to the reaction and vibration of the injector pulses. The tight fit of the injector alone in ther bosses would probably do this job, but no-one in their right mind would take such a stupid chance.
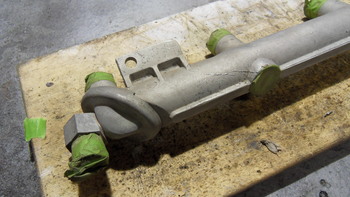
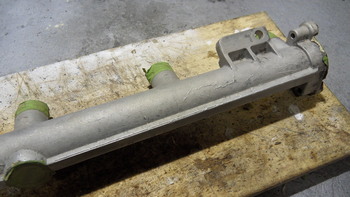
The fixing brackets were then trimmed of the excess bolting pad material. I elected not to trim all the excess bracket web off - spreading the load over a bit more vessel wall is prudent.
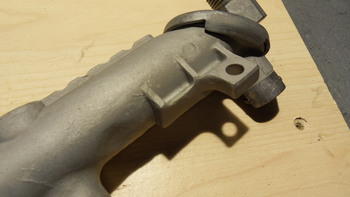
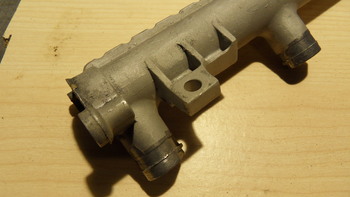
The design of the part makes me think a version of this casting is used on other engines in the GM range.
From measurements on the inside of the rail the rib on the top around the threaded fitting is more of a casting convenience than a structural design feature so I scalloped it. If I can get to a mill before I fit it i'll shave it down more and just leave some thickness around the fitting.
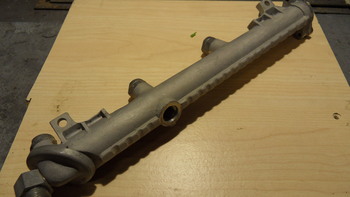
Fina weight 0.607kg. 0.016kg saved.
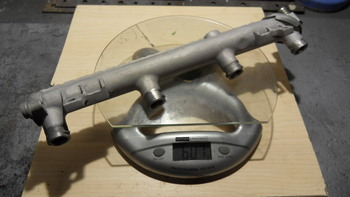
Totally worth it.