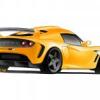
Hub Carrier Bolts And Toe Links - Service Requirement - Important For
#81
Posted 07 February 2017 - 05:42 PM
#82
Posted 07 February 2017 - 07:02 PM
#83
Posted 07 February 2017 - 07:16 PM
#84
Posted 07 February 2017 - 07:18 PM
#85
Posted 07 February 2017 - 07:24 PM
#86
Posted 07 February 2017 - 07:33 PM
sounds like someone needs a bit of vagisil.
#87
Posted 07 February 2017 - 07:39 PM
Spitfire for toelinks. Just ordered mine.
#88
Posted 07 February 2017 - 07:42 PM
Oops forgot to put any text with the photo. Anyway just a little pictorial as regards the HCB's, these 2 are fronts, but as you can see, the long one is as clean as a whistle, the short one however is fairly heavily corroded at the midway point,, and must have some impact on its strength, just goes to show that you should be changing them out with some regularity.
The failure point on the snapped ones is on the non-threaded shank of the longer bolts (in my case and on another that I asked the owner about).
To eliminate that rust issue, use either stainless shims or aluminium shims (as I do) instead of the Lotus' "optimum" rust inducing mild steel. Another example of where the Lotus parts are sub-optimum, not that I think that rust is serious enough to weaken the bolt great deal.
Having said that it did strike me that a build of up rust + salt between the many layers of the shims might cause extra tension on the bolts. This is why I'd recommend a more inert shim material. Ideally, making a single shim of the correct thickness is better than a stack of multiple shims, as it reduces the number of failure/slippage points and also reduces the risk of rust/salt crystal build up between the layers.
Ooof! Some care needs to be taken Nev. The shims need to be a certain hardness so aluminium will need to be VERY carefully selected for the right grade and is itself prone to corrosion especially when in contact with iron like suspension parts. Stainless will likely cause corrosion in other bits... like the bolts....through galvanic corrosion.
I use the lotus shims (which come plated and passivated) along with a smear of anticorrosion grease to help prevent rust. Eventually they will rust but they are cheap enough to replace.
#89
Posted 07 February 2017 - 07:49 PM
#90
Posted 07 February 2017 - 07:54 PM
Well said FLD, the voice of reason. I think your chosen path is optimum.Ooof! Some care needs to be taken Nev. The shims need to be a certain hardness so aluminium will need to be VERY carefully selected for the right grade and is itself prone to corrosion especially when in contact with iron like suspension parts. Stainless will likely cause corrosion in other bits... like the bolts....through galvanic corrosion. I use the lotus shims (which come plated and passivated) along with a smear of anticorrosion grease to help prevent rust. Eventually they will rust but they are cheap enough to replace.
The failure point on the snapped ones is on the non-threaded shank of the longer bolts (in my case and on another that I asked the owner about). To eliminate that rust issue, use either stainless shims or aluminium shims (as I do) instead of the Lotus' "optimum" rust inducing mild steel. Another example of where the Lotus parts are sub-optimum, not that I think that rust is serious enough to weaken the bolt great deal. Having said that it did strike me that a build of up rust + salt between the many layers of the shims might cause extra tension on the bolts. This is why I'd recommend a more inert shim material. Ideally, making a single shim of the correct thickness is better than a stack of multiple shims, as it reduces the number of failure/slippage points and also reduces the risk of rust/salt crystal build up between the layers.Oops forgot to put any text with the photo. Anyway just a little pictorial as regards the HCB's, these 2 are fronts, but as you can see, the long one is as clean as a whistle, the short one however is fairly heavily corroded at the midway point,, and must have some impact on its strength, just goes to show that you should be changing them out with some regularity.
#91
Posted 07 February 2017 - 08:36 PM
#92
Posted 07 February 2017 - 08:36 PM
#93
Posted 07 February 2017 - 10:07 PM
Oops forgot to put any text with the photo. Anyway just a little pictorial as regards the HCB's, these 2 are fronts, but as you can see, the long one is as clean as a whistle, the short one however is fairly heavily corroded at the midway point,, and must have some impact on its strength, just goes to show that you should be changing them out with some regularity.
The failure point on the snapped ones is on the non-threaded shank of the longer bolts (in my case and on another that I asked the owner about).
To eliminate that rust issue, use either stainless shims or aluminium shims (as I do) instead of the Lotus' "optimum" rust inducing mild steel. Another example of where the Lotus parts are sub-optimum, not that I think that rust is serious enough to weaken the bolt great deal.
Having said that it did strike me that a build of up rust + salt between the many layers of the shims might cause extra tension on the bolts. This is why I'd recommend a more inert shim material. Ideally, making a single shim of the correct thickness is better than a stack of multiple shims, as it reduces the number of failure/slippage points and also reduces the risk of rust/salt crystal build up between the layers.
Ooof! Some care needs to be taken Nev. The shims need to be a certain hardness so aluminium will need to be VERY carefully selected for the right grade and is itself prone to corrosion especially when in contact with iron like suspension parts. Stainless will likely cause corrosion in other bits... like the bolts....through galvanic corrosion.
I use the lotus shims (which come plated and passivated) along with a smear of anticorrosion grease to help prevent rust. Eventually they will rust but they are cheap enough to replace.
Any place better than another for the lotus shims ?
#94
Posted 07 February 2017 - 10:13 PM
I'm not ruling "Spitfire" out, I'm just trying to see what other options are out there, so I can then make the Optimum choice. 🈲
OE
Elise Parts
Elise Shop
Phoenix (still made?)
Nitron (still made?)
Edited by WrightStuff, 07 February 2017 - 10:15 PM.
#95
Posted 07 February 2017 - 11:08 PM
Does the grease not reduce the friction of the mating faces of the joint? You fit higher spec bolts to increase the torque to maintain a higher clamp load on the joint surely you want to maintain that Friction? And going back a few posts on the other thread related to hcb's isnt the shear strength directly related to the ultimate tensile strength?Well said FLD, the voice of reason. I think your chosen path is optimum.Ooof! Some care needs to be taken Nev. The shims need to be a certain hardness so aluminium will need to be VERY carefully selected for the right grade and is itself prone to corrosion especially when in contact with iron like suspension parts. Stainless will likely cause corrosion in other bits... like the bolts....through galvanic corrosion. I use the lotus shims (which come plated and passivated) along with a smear of anticorrosion grease to help prevent rust. Eventually they will rust but they are cheap enough to replace.
The failure point on the snapped ones is on the non-threaded shank of the longer bolts (in my case and on another that I asked the owner about). To eliminate that rust issue, use either stainless shims or aluminium shims (as I do) instead of the Lotus' "optimum" rust inducing mild steel. Another example of where the Lotus parts are sub-optimum, not that I think that rust is serious enough to weaken the bolt great deal. Having said that it did strike me that a build of up rust + salt between the many layers of the shims might cause extra tension on the bolts. This is why I'd recommend a more inert shim material. Ideally, making a single shim of the correct thickness is better than a stack of multiple shims, as it reduces the number of failure/slippage points and also reduces the risk of rust/salt crystal build up between the layers.Oops forgot to put any text with the photo. Anyway just a little pictorial as regards the HCB's, these 2 are fronts, but as you can see, the long one is as clean as a whistle, the short one however is fairly heavily corroded at the midway point,, and must have some impact on its strength, just goes to show that you should be changing them out with some regularity.
Edited by stevey.d, 07 February 2017 - 11:09 PM.
#96
Posted 08 February 2017 - 12:59 AM
Does the grease not reduce the friction of the mating faces of the joint? You fit higher spec bolts to increase the torque to maintain a higher clamp load on the joint surely you want to maintain that Friction? And going back a few posts on the other thread related to hcb's isnt the shear strength directly related to the ultimate tensile strength?
Well said FLD, the voice of reason. I think your chosen path is optimum.
Ooof! Some care needs to be taken Nev. The shims need to be a certain hardness so aluminium will need to be VERY carefully selected for the right grade and is itself prone to corrosion especially when in contact with iron like suspension parts. Stainless will likely cause corrosion in other bits... like the bolts....through galvanic corrosion. I use the lotus shims (which come plated and passivated) along with a smear of anticorrosion grease to help prevent rust. Eventually they will rust but they are cheap enough to replace.
The failure point on the snapped ones is on the non-threaded shank of the longer bolts (in my case and on another that I asked the owner about). To eliminate that rust issue, use either stainless shims or aluminium shims (as I do) instead of the Lotus' "optimum" rust inducing mild steel. Another example of where the Lotus parts are sub-optimum, not that I think that rust is serious enough to weaken the bolt great deal. Having said that it did strike me that a build of up rust + salt between the many layers of the shims might cause extra tension on the bolts. This is why I'd recommend a more inert shim material. Ideally, making a single shim of the correct thickness is better than a stack of multiple shims, as it reduces the number of failure/slippage points and also reduces the risk of rust/salt crystal build up between the layers.Oops forgot to put any text with the photo. Anyway just a little pictorial as regards the HCB's, these 2 are fronts, but as you can see, the long one is as clean as a whistle, the short one however is fairly heavily corroded at the midway point,, and must have some impact on its strength, just goes to show that you should be changing them out with some regularity.
That was my immediate thought when it was mentioned. There was a previous thread (same one?) some time ago where someone explained that the friction created on the mating faces by the clamping force of the bolts is an important component of the joint. That being correct, would not grease on the mating surfaces compromise that friction?
#97
Posted 08 February 2017 - 09:08 AM
Oops forgot to put any text with the photo. Anyway just a little pictorial as regards the HCB's, these 2 are fronts, but as you can see, the long one is as clean as a whistle, the short one however is fairly heavily corroded at the midway point,, and must have some impact on its strength, just goes to show that you should be changing them out with some regularity.
The failure point on the snapped ones is on the non-threaded shank of the longer bolts (in my case and on another that I asked the owner about).
To eliminate that rust issue, use either stainless shims or aluminium shims (as I do) instead of the Lotus' "optimum" rust inducing mild steel. Another example of where the Lotus parts are sub-optimum, not that I think that rust is serious enough to weaken the bolt great deal.
Having said that it did strike me that a build of up rust + salt between the many layers of the shims might cause extra tension on the bolts. This is why I'd recommend a more inert shim material. Ideally, making a single shim of the correct thickness is better than a stack of multiple shims, as it reduces the number of failure/slippage points and also reduces the risk of rust/salt crystal build up between the layers.
Ooof! Some care needs to be taken Nev. The shims need to be a certain hardness so aluminium will need to be VERY carefully selected for the right grade and is itself prone to corrosion especially when in contact with iron like suspension parts. Stainless will likely cause corrosion in other bits... like the bolts....through galvanic corrosion.
I use the lotus shims (which come plated and passivated) along with a smear of anticorrosion grease to help prevent rust. Eventually they will rust but they are cheap enough to replace.
I've had alu home made shims on the car for about 3 years now and there is no issue that I can see or had whilst driving over very rough roads with a relatively heavy car at speed. The softness of the alu face is a benefit IMO, as I rough up the mating surface with grit paper to ensure a stronger key to the iron uprights. The alu shim blocks themselves will not compress and I've had them on and off many many times (for geoing) and inspected them carefully. There is no noticeable galvanic corrosion either after 2 or 3 years, so I think the assembly is fairly free of this issue.
I've had a think about the forces acting on the HCB and the 2 faces they mate. The main and overwhelming force will be vertical sheer IMO, there will be relatively little compressive force on the spacers.
I have aluminium hub carriers on the front of my car and it's worth noting they are also happy with the compressive clamping force (same as my alu shims).
If you are worried about stainless shims, then you better write an email to Elise Parts, as that is what they sell. Theirs are extra shiny and polished to help make matter worse IMO. I rubbed them down with a file and grit paper to alleviate this.
Edited by Nev, 08 February 2017 - 09:24 AM.
#98
Posted 08 February 2017 - 09:31 AM
Does the grease not reduce the friction of the mating faces of the joint? You fit higher spec bolts to increase the torque to maintain a higher clamp load on the joint surely you want to maintain that Friction? And going back a few posts on the other thread related to hcb's isnt the shear strength directly related to the ultimate tensile strength?
Well said FLD, the voice of reason. I think your chosen path is optimum.
Ooof! Some care needs to be taken Nev. The shims need to be a certain hardness so aluminium will need to be VERY carefully selected for the right grade and is itself prone to corrosion especially when in contact with iron like suspension parts. Stainless will likely cause corrosion in other bits... like the bolts....through galvanic corrosion. I use the lotus shims (which come plated and passivated) along with a smear of anticorrosion grease to help prevent rust. Eventually they will rust but they are cheap enough to replace.
The failure point on the snapped ones is on the non-threaded shank of the longer bolts (in my case and on another that I asked the owner about). To eliminate that rust issue, use either stainless shims or aluminium shims (as I do) instead of the Lotus' "optimum" rust inducing mild steel. Another example of where the Lotus parts are sub-optimum, not that I think that rust is serious enough to weaken the bolt great deal. Having said that it did strike me that a build of up rust + salt between the many layers of the shims might cause extra tension on the bolts. This is why I'd recommend a more inert shim material. Ideally, making a single shim of the correct thickness is better than a stack of multiple shims, as it reduces the number of failure/slippage points and also reduces the risk of rust/salt crystal build up between the layers.Oops forgot to put any text with the photo. Anyway just a little pictorial as regards the HCB's, these 2 are fronts, but as you can see, the long one is as clean as a whistle, the short one however is fairly heavily corroded at the midway point,, and must have some impact on its strength, just goes to show that you should be changing them out with some regularity.
That was my immediate thought when it was mentioned. There was a previous thread (same one?) some time ago where someone explained that the friction created on the mating faces by the clamping force of the bolts is an important component of the joint. That being correct, would not grease on the mating surfaces compromise that friction?
The friction for the clamping force is generated by the threaded section. You don't want to "waste" torque overcoming frictional resistances on the bolt's head (against rust and dirt in the upright recess) , otherwise the torque on the threaded section is reduced, and hence your clamping force is reduced. I found that the recesses where the bolt heads mate to the iron were hard to get at and clean, hence why I did this.
If you are able to clean the head recesses this won't be a problem I am sure, the thread section is obviously easy to clean out, but getting a flat and clean surface for the bolt head to mate too was trickier.
Torque critical assemblies like ARB head bolts and flywheel bolts etc use lube for this reason.
Edited by Nev, 08 February 2017 - 09:38 AM.
#99
Posted 08 February 2017 - 01:33 PM
Does the grease not reduce the friction of the mating faces of the joint? You fit higher spec bolts to increase the torque to maintain a higher clamp load on the joint surely you want to maintain that Friction? And going back a few posts on the other thread related to hcb's isnt the shear strength directly related to the ultimate tensile strength?
Well said FLD, the voice of reason. I think your chosen path is optimum.
Ooof! Some care needs to be taken Nev. The shims need to be a certain hardness so aluminium will need to be VERY carefully selected for the right grade and is itself prone to corrosion especially when in contact with iron like suspension parts. Stainless will likely cause corrosion in other bits... like the bolts....through galvanic corrosion. I use the lotus shims (which come plated and passivated) along with a smear of anticorrosion grease to help prevent rust. Eventually they will rust but they are cheap enough to replace.
The failure point on the snapped ones is on the non-threaded shank of the longer bolts (in my case and on another that I asked the owner about). To eliminate that rust issue, use either stainless shims or aluminium shims (as I do) instead of the Lotus' "optimum" rust inducing mild steel. Another example of where the Lotus parts are sub-optimum, not that I think that rust is serious enough to weaken the bolt great deal. Having said that it did strike me that a build of up rust + salt between the many layers of the shims might cause extra tension on the bolts. This is why I'd recommend a more inert shim material. Ideally, making a single shim of the correct thickness is better than a stack of multiple shims, as it reduces the number of failure/slippage points and also reduces the risk of rust/salt crystal build up between the layers.Oops forgot to put any text with the photo. Anyway just a little pictorial as regards the HCB's, these 2 are fronts, but as you can see, the long one is as clean as a whistle, the short one however is fairly heavily corroded at the midway point,, and must have some impact on its strength, just goes to show that you should be changing them out with some regularity.
That was my immediate thought when it was mentioned. There was a previous thread (same one?) some time ago where someone explained that the friction created on the mating faces by the clamping force of the bolts is an important component of the joint. That being correct, would not grease on the mating surfaces compromise that friction?
Just confirm Nev, you are using the 12.9 bolts on ally uprights?
#100
Posted 08 February 2017 - 01:38 PM
0 user(s) are reading this topic
0 members, 0 guests, 0 anonymous users